At least half the questions and emails I get from readers, are about LEADING. I have been getting comments that the Tape Tip Instructions are not working for some of our readers. I consider the Tape Tip so essential to happy Gallery Glass crafting that I am on a mission to update and expand on the instructions until every last one of you emails me and says, "Yes, I can make it, now!"
Preparing the Cap: First, remove the seal from inside the cap, replace the cap and use a craft knife to CUT the tip off the end of the Gallery Glass Cap. Cut down about 1/4" from the top, but don't cut past the ridge that holds the small clear cap on the bottle. (Just be sure to cut off the thick plastic at the very end of the cap. ) This tip can be used over and over again. Just be sure to clean it out and add a new tape tip every time you begin a new leading project. You can move this tip from bottle to bottle as you use up the leading--to save time.
Step One -
Position the tape: Pull off a 3 1/2" strip of 3/4" wide cellophane tape (Scotch 3/4" Magic Tape #810 is good). Place the left edge of the tape at an angle starting at the center of the cap (see diagram 1). Press the tape to the cap as you rotate the bottle, securing the first turn of the tape all the way to the end of the cap to prevent leakage. (This is very important, tape must be TIGHT at the end for the next step to work "turn" correctly. You may need to pull and stretch it slightly for the hole to be small enough and for it to begin the turn in the next step.)
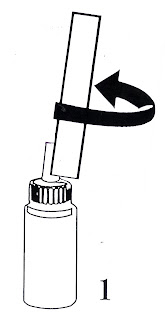
The angle shown will give you a small bead. If you wish to increase the size of the bead of leading--increase the angle to the RIGHT. Be sure to leave the bottom of the tape positioned right in the very center of the tip as shown in the illustration, but position the TOP of the tape more to the right. I will sometimes un-wind and re-wind a piece of tape several time until the hole is exactly the size I want the bead to be. Experience will tell you which size hole works best for the intricacy of your design. The more intricate designs require a smaller bead in order to preserve that intricacy.
Step 2 - Forming the Cone: As you turn the bottle in your left hand, and adhere the tape tightly with your right, the tape will form a cone (see diagram 2). Press tape to the cap firmly at the TOP as the tape changes direction to make the hole firm and secure. If the tape is loose, and doesn't turn--unwind and start again. Continue turning the bottle in your left hand and adhering the tape to previous layers with your right. This is the time to check the size of the hole you have made. Make adjustments if it is too small or too large. Un-wind and adjust the ANGLE (see step 1) of the tape- right makes it larger, left makes it smaller.
Step 3 - Reversing directions and reinforcing the tip: If the previous steps have been done correctly, the tape will reverse directions and reinforce the tip. Continue to turn the bottle in your left hand and allow tape to wind down. Keep it tight. Press any extra tape over the side of the cap to make a "tab" for easy removal later. Hole size can be further adjusted at this point. If the hole is too small, but the tip is good, snip the cone 1/8" to make a larger hole, although you shouldn't have to do this if you have adjusted the ANGLE of the tape in step 1.
Now let's talk about the leading bottle. There are 3 sizes of Liquid Leading. The 2 oz. bottle is a good size for kits, but not as economical as the 8 oz. size. The 4 oz. bottle is softer than the other two bottles because it is purchased primarily for Liquid Leading. It is the most popular size because it fits the hand perfectly and is easier to squeeze. I use the same 4 oz. bottle over and over because I can fill it from the 8 oz. bottle. Cut off the cap of the 8 oz. bottle above the ridge (Preparing the Cap - see above) and squeeze the leading into the 4 oz. bottle from the altered tips. Continue to re-fill the 4 oz. until all the leading is gone out of the larger size. Not only does this method save money, but it softens and thins the leading as it goes through the altered cap of the 8 oz. and this almost totally eliminates the "plops" of unexpected air that is the primary complaint of Gallery Glass artists.
Please let me know about the problems you encounter as you try to make this tip. The Tape Tip effectively controls the flow, gives you an infinite variety of bead sizes, and makes the leading easier to squeeze out of the bottle. What's NOT to like?
Leading of Modular Designs, Suncatchers and Leading Strips
Now, let's explore another leading situation--one where you will dispense the leading straight from the bottle. This method will be used for non-intricate suncatchers, the components of a window that is to be completed in the modular method and of course the making of straight lead strips for connecting the modules on the window.
To begin, place smooth side of Leading Blank under pattern. Tape pattern to back of blank. Arrange all elements under sheets. If Leading Blanks are not available, you can tape the pieces to cardboard sized to fit inside a food storage bag. Do the elements on the outside of the bag.
1. Remove cap and seal from Liquid Leading. Push the curved end of the metal tool into bottle about 1/2" and twist around to make a large hole. Do not cut tip. Replace small cap on tip. Turn the bottle upside down and tap on a hard surface to force leading into the tip. Remove small cap.
2. Hold the bottle vertically, "broom handle" style, making sure the tip of the leading bottle does not touch the leading surface. Do not rest your elbow on your work surface, it will inhibit your movement. Squeeze leading (1/8" to 3/16" in diameter) on the Leading Blank over the solid lines of the pattern taped underneath. When you get near the end of your line, stop squeezing and lower the bottle tip to the leading surface to prevent blobs of leading. Continue until all elements of the design have been outlined.
3. Leading Strips: Use a sheet of lined notebook paper as a pattern for creating leading lines. Tape to back of Leading Blank. Let Liquid Leading dry approximately 8 hours or until leading strips peel up smoothly. Window Color and liquid Leading paints can only be air dried. Do not try to hasten dry time with hair dryer or fan.
Quick Reference Leading Tips
Messy Lines: Uniform lines are achieved by holding the leading tip above the leading surface and coordinating pressure on the bottle with forward movement of the bottle. Practice on notebook paper until you have mastered this rhythm.
Beginning Bumps: Anchor the leading to the Gallery Glass blank or leading surface so leading will not curl up around the tip and create a bump before beginning the line. Wipe tip with a
paper towel and anchor aw you begin to squeeze.
Ending Bumps: Stop squeezing earlier before reaching the end of the line--bring tip down allowing lead to end, or to join a previously leaded line.
Correcting Mistakes: This is easier after the leaded outline is dry. Use a toothpick to gently pull up only the unwanted portion of the outline and trim it away with small scissors. Press the remaining lead firmly back down to the surface.